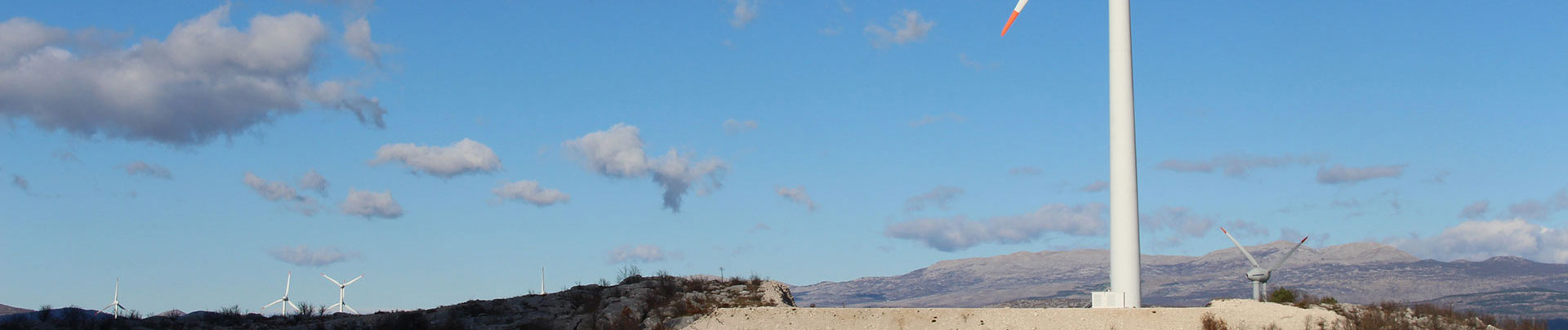
Innovations
Integrated monitoring and management system
ZaCjel - Brošura_1631105921.pdf
Download PDFTo offer the industry a unique solution, scientists are developing an innovative comprehensive system for monitoring and managing dynamically loaded structures to preserve their integrity and prevent damage in order to increase their reliability, safety and service life with reduced maintenance costs. An intelligent solution developed for the industry will make it easier for users to manage structures and plants
Mechanical structures are becoming more complex, and the requirements that are set in the design and exploitation in terms of efficiency, safety and reliability are an increasing challenge. The load-bearing capacity of structures decreases during their service life due to aging of the material due to fatigue, corrosion, perforation and other degradation mechanisms. Accumulation of damage and growth of cracks in the material can lead to loss of integrity, ie the integrity of an individual component or the entire structure.
Depending on the type of construction, such phenomena can have catastrophic consequences. Structural Health Monitoring (SHM) systems ensure their safety and reliability, enable the design of demanding dynamically loaded structures and reduce management and maintenance costs. Such systems are automated to continuously monitor the condition of the structure and detect damage with minimal intervention. Among the most important tasks of the SHM system are damage detection, localization and quantification, with an estimate of the remaining service life.
In recent years, "intelligent" or "active" systems have been developed, which collect the appropriate responses of the structure and react in a predetermined manner at a given time. These systems are composed of passive and active elements, which act as sensors and actuators. The use of intelligent monitoring and control systems is necessary in power plants, transport and other systems in which structural components are dynamically loaded such as wind turbines, turbines, generators, piston machines, process plant parts, road, rail and other vehicles, conveyors and the like. In addition, as the required service life of complex dynamically loaded structures is quite long, it requires the application of advanced numerical and experimental methods for more realistic simulation of the material defining process, as well as for the development of new materials with better mechanical properties.
Despite the need and demand, there is currently no product on the market that offers industry (in Croatia and beyond) a unified solution for a systematic approach to the preservation of structures and their better exploitation, but experts combine different products for supervision and separately for structural management.
An intelligent monitoring and management system developed as part of the ZaCjel project will make it easier for users to manage structures and plants. The potential for use in industry is wide. In collaboration with industry, scientists can develop and expand the initial application of the system and personalize it through joint projects and adapt it to individual needs.
What does the research team offer to the industry?
- Field and laboratory measurements of vibrations of mechanical structures
- Monitoring the condition of structures and plants,
- Design and preparation of studies and calculations of strength, stability, structural integrity and system dynamics,
- Design of systems for management and protection of structural integrity
- Other activities related to industries where the primary activity is closely related to dynamically loaded structures.
Competitive advantages of the new system:
- Increasing the efficiency and reliability and extending the service life of structures by more precisely defining the permitted operating modes
- More effective monitoring of the occurrence and growth of damage in structural components
- optimal placement of the monitoring system sensor
- Improving equipment maintenance plans
- Reducing equipment maintenance costs
- Reduction of potential costs caused by downtime in system operation.